Quick and Reliable Packaging Equipment Repair Service Solutions to Minimize Downtime
In the affordable landscape of manufacturing, the effectiveness of product packaging procedures hinges on the reliability of equipment. Quick and reputable fixing solutions are vital in reducing downtime, which can lead to substantial functional setbacks and economic losses.
Importance of Timely Repair Works
Timely repair work of packaging devices are vital for preserving functional effectiveness and reducing downtime. In the hectic environment of manufacturing and product packaging, even minor malfunctions can lead to substantial hold-ups and efficiency losses. Resolving concerns immediately makes certain that devices operate at their optimum ability, consequently securing the flow of operations.
In addition, regular and timely maintenance can protect against the rise of minor problems right into significant malfunctions, which typically incur greater repair costs and longer downtimes. An aggressive technique to device fixing not just preserves the integrity of the equipment however also enhances the general reliability of the manufacturing line.
Furthermore, timely repair services add to the long life of packaging equipment. Makers that are serviced promptly are much less likely to deal with excessive damage, allowing organizations to maximize their financial investments. This is especially crucial in industries where high-speed product packaging is important, as the demand for consistent efficiency is paramount.
Advantages of Reliable Company
Reliable solution providers play an essential duty in guaranteeing the smooth procedure of product packaging devices. Their expertise not only boosts the performance of repair work yet additionally contributes substantially to the long life of equipment. Reputable solution carriers are geared up with the technical expertise and experience essential to diagnose issues precisely and carry out reliable solutions rapidly. This minimizes the danger of reoccuring troubles and ensures that devices operate at optimal performance levels.
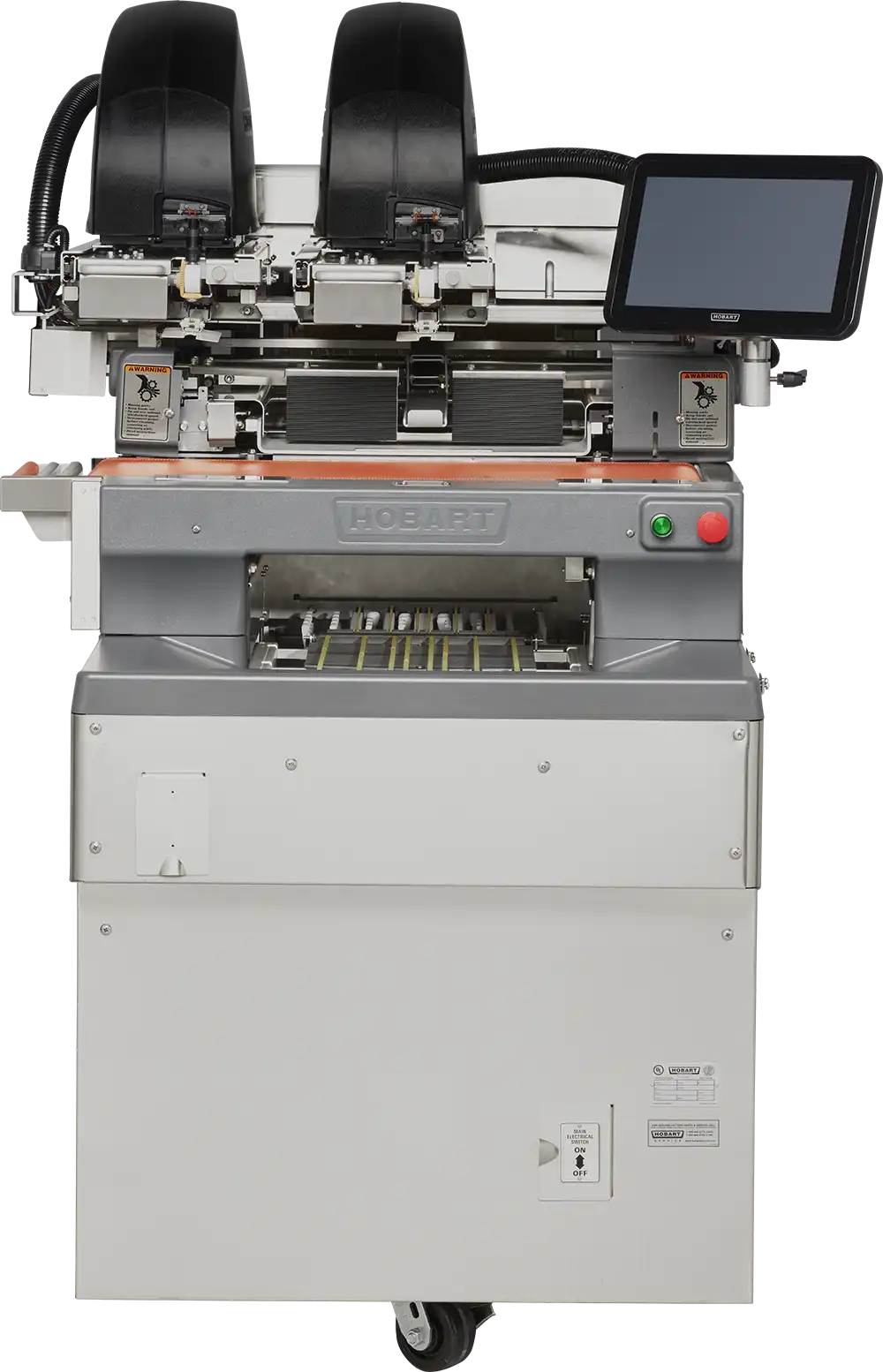
Furthermore, a reputable service provider offers extensive support, including training and advice for team on equipment procedure and upkeep finest methods. This not only empowers staff members yet additionally grows a culture of safety and efficiency within the company. On the whole, the advantages of engaging dependable provider expand beyond immediate repairs, favorably affecting the entire operational operations of packaging processes.
Usual Product Packaging Device Issues
In the world of packaging procedures, various issues can endanger the effectiveness and performance of equipments (packaging machine repair). Another usual issue is misalignment, which can create jams and uneven packaging, influencing product high quality and throughput.
Electric problems can likewise interfere with product packaging operations. Damaged wiring or malfunctioning sensors might cause erratic maker actions, causing delays and boosted functional costs. Additionally, software program problems can prevent the device's programs, leading to operational ineffectiveness.
Irregular item click this link circulation is an additional vital problem. This can emerge from variations in product form, weight, or dimension, which might influence the machine's ability to deal with items precisely. Lastly, inadequate training of operators can worsen these issues, as untrained workers may not acknowledge early signs of malfunction or may abuse the tools.
Resolving these typical packaging device issues promptly is important to maintaining performance and making sure a smooth operation. Regular inspections and aggressive upkeep can considerably reduce these concerns, cultivating a reliable product packaging atmosphere.
Tips for Reducing Downtime
To minimize downtime in product packaging operations, implementing an aggressive maintenance strategy is critical. Consistently arranged maintenance checks can recognize prospective concerns before they escalate, making certain equipments operate efficiently. Developing a routine that consists of lubrication, calibration, and assessment of crucial parts can substantially reduce the regularity of unexpected malfunctions.
Training personnel to operate machinery appropriately and acknowledge very early indication of malfunction can likewise play a vital function. Encouraging operators with the expertise to perform fundamental troubleshooting can protect against minor concerns from causing major hold-ups. Moreover, preserving an efficient inventory of necessary spare parts can quicken repairs, as waiting on components can lead to prolonged downtime.
Additionally, documenting maker efficiency and upkeep activities can help determine patterns and recurring problems, enabling targeted interventions. Integrating innovative surveillance technologies can provide real-time data, allowing predictive maintenance and lessening the danger of abrupt failings.
Last but not least, cultivating open interaction in between drivers and upkeep teams makes certain that any kind of abnormalities are without delay reported and addressed. By taking these proactive measures, businesses can enhance functional performance and dramatically lower downtime in product packaging procedures.
Picking the Right Repair Service Solution
Picking the suitable repair solution for packaging equipments is an important decision that can significantly affect operational effectiveness. Begin by evaluating the copyright's experience with your certain kind of packaging tools.
Next, consider the provider's track record. Looking for comments from various other companies within your sector can provide understandings right into dependability and top quality. Qualifications and partnerships with acknowledged tools producers can additionally indicate a commitment to quality.
Additionally, examine their response time and accessibility. A service supplier who can use prompt support decreases downtime and keeps manufacturing circulation stable. It's additionally important to inquire regarding service warranty and service index assurances, which can reflect the confidence the supplier has in their job.
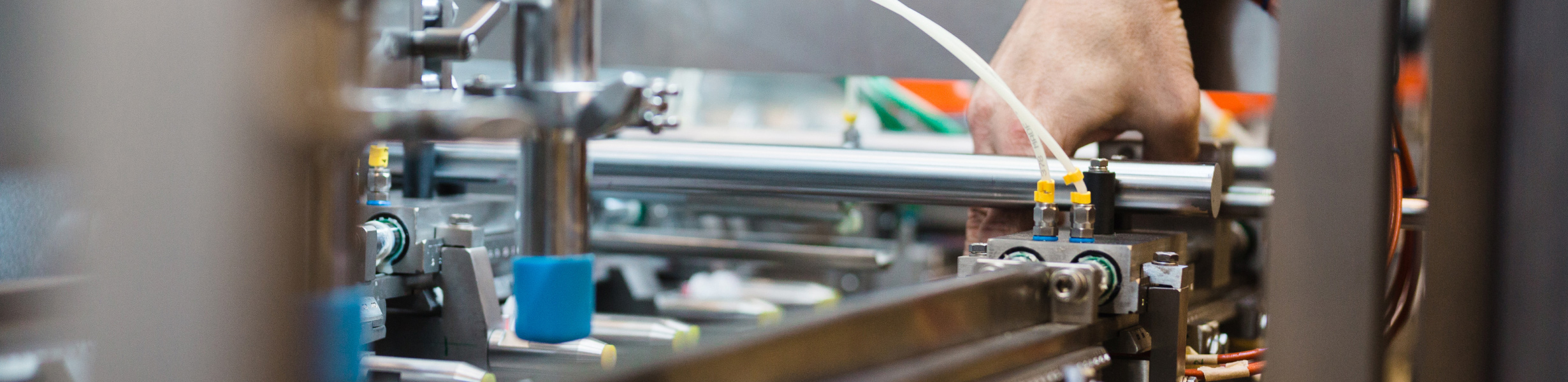
Conclusion
In final thought, the value navigate to these guys of trusted and quick packaging device repair service solutions can not be overemphasized, as they play an essential duty in lessening downtime and ensuring operational effectiveness. Carrying out proactive upkeep practices and investing in personnel training further enhances the longevity of product packaging equipment.
Timely repairs of packaging equipments are essential for maintaining operational effectiveness and lessening downtime.In addition, timely repair services add to the long life of product packaging equipment. Generally, the advantages of engaging reputable solution suppliers prolong beyond immediate repairs, positively impacting the whole functional process of product packaging processes.

Comments on “Get Fast and Efficient Packaging Machine Repair for Your Production Line”